Mit Glas oder Kunststoff lassen sich, je nach Verfahren, schon heute flexible bendale OLEDs herstellen, dünne und durchsichtige filigrane Screens. Mit Edelstahl als Substrat wären keine transparenten OLED-Displays umsetzbar – dafür aber andere Anwendungen oder Produkte, bei denen die Robustheit eine sehr große Rolle spielt.
Möglich machen dies neue anwendungsbezogene Forschungsarbeiten des Fraunhofer-Institut für Organische Elektronik, Elektronenstrahl- und Plasmatechnik (FEP), die in Zusammenarbeit mit Nippon Steel & Sumikin Materials Co. Ltd. (NSMAT) und Nippon Steel & Sumitomo Metal Corporation (NSSMC) entstanden sind.
Schon jetzt ist Edelstahl nicht nur bei Küchengeräten oder Anlagenrohren ein oft genutzter Werkstoff. Denn seit einigen Jahren werden Edelstahlfolien auch für Dünnfilm-Photovoltaik und -Batterien verwendet. Bald soll Edelstahl als Substrat auch in flexiblen elektronischen Bauelementen Anwendung finden.
Aufgrund der von NSSMC entwickelten Planarisierungsschicht und der vergleichsweise guten thermischen Leitfähigkeit von Edelstahl sind homogene großflächige Leuchtflächen mit guter Wärmeableitung und der Betrieb unter Stromdichten > 10 mA/cm² einfacher realisierbar, so die Forscher. Bedeutet: große Lighting-flächen lassen sich damit einfach umsetzen.
Vorteil: Da OLED vor Feuchtigkeit und Sauerstoff geschützt werden müssen, damit die organischen Schichten funktionstüchtig bleiben, sind durch die hervorragende Barrierewirkung des Edelstahls gegen Umwelteinflüsse auch Anwendungen denkbar, die es noch nicht oder so noch nicht gibt.
Einen Blick in die Glas-, pardon: Edelstahl-Kugel, gibt Jun Nakatsuka, Manager Business Developement bei NSMAT: „Durch die gute Glätte und aufgrund der hohen thermischen Leitfähigkeit der Edelstahlfolie erreichen wir ein sehr homogenes OLED-Licht. In drei Jahren sehen wir vielleicht schon OLED auf Edelstahl in Autos als Blinker oder Rücklicht, in Fassadenverkleidungen oder in Displays.“
Damit wären künftig große OLED-Medienfassaden denkbar. Die wiederum könnten mit ihren exzellenten Schwarzwerten punkten, die im Vergleich zu LED oder LCD hervorragend sind. Als Vision: Vielleicht gäbe es dann in der Dubai Mall den größten OLED-Screen der Welt – und an der Außenfassade den ersten oder den größten OLED-Outdoor-Screen der Welt.
Bis es soweit ist, muss allerdings noch weiter geforscht, entwickelt und optimiert werden. Nach der aufwändigen Entwicklung der Edelstahlfolie, soll diese nun produktionstauglich gemacht werden. Das Fraunhofer FEP verfügt über eine Rolle-zu-Rolle-Prozesslinie zur Herstellung von OLED auf flexiblen Materialien und einen reproduzierbaren OLED-Prozess. Dies macht die Optimierung der Edelstahlfolie mit einer Polymer-Glättungsschicht erst möglich.
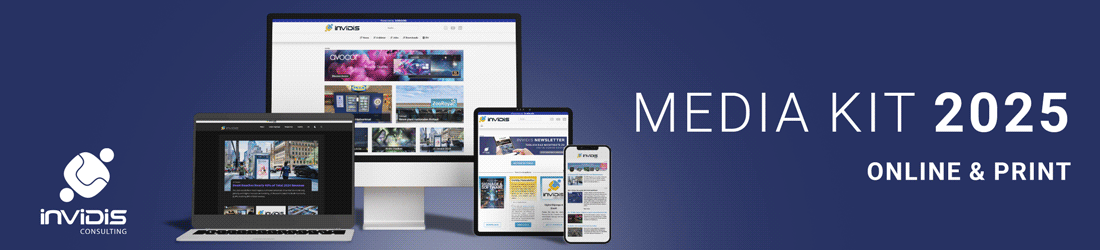