Technologisch sind die Entwickler und Ingenieure soweit: Gedruckte OLED-Panels könnten schon bald in die Großserienproduktion gehen. Und sollen sie auch, wenn es nach dem japanischen Hersteller JOLED geht, der dieses Herstellungsverfahren für das beste und zugleich kostengünstigste hält. Erste Serienprodukte haben die JOLED-Fabriken gerade erst verlassen. Sie werden aber bislang lediglich für Spezialanwendungen genutzt, in dem Falle für Medical Screens von Sony, die höchstwahrscheinlich auch erst einmal nur für den japanischen Markt gedacht sind. Sony ist nicht nur Kunde von JOLED – sondern mit Panasonic eines der beiden Unternehmen, die Bereiche ausgegliedert und als JOLED neu gegründet haben.
Die Sony-Screens (vgl. Aufmacherbild) lösen mit 3.840 x 2.160p auf. Sie sind die weltweit ersten Displays, die Panels nutzen, die nach dem Druckverfahren genutzt werden. Damit erreichen die 21,6-Zöller einen Wert von 204 PPI. Mit 1,3 mm sind diese Displays extrem dünn. Das Gewicht liegt bei 500 Gramm. Die maximale Luminanz beträgt 350 cd/m². Als Kontrastwert werden von JOLED 1.000.000:1 angegeben.
Der ganz große Wurf blieb für JOLED bislang aus. Denn derzeit hapert es auch am frischen Kapital, das die Firma benötigt. Wir berichtet, ist JOLED auf der Suche nach einem Investor. Und besonders gerne wäre man gemeinsam mit JDI eine Liaison eingegangen. Da aber bei JDI derzeit auch nicht alles so läuft, wie geplant, schaut sich JOLED auch anderweitig um. Laut Nikkei Asian Review hätte man gerne schon im Oktober 2017 einen Investor gefunden. Nun hofft man, dies im ersten Quartal 2018 zu schaffen. So äußerte sich jedenfalls CTO Yoneharu Takubo auf einer Pressekonferenz in Tokio.
Gesucht würden japanische Investoren, die 100 Milliarden Yen investieren – umgerechnet derzeit etwa 748,5 Millionen Euro. Damit löst man sich möglicherweise von dem Plan, dass JDI 51% der Anteile übernimmt. Denn zuletzt hatte es geheißen, dass JDI bis Juni 2018 einsteigen wollte. Derzeit ist JDI schon mit 15% an JOLED beteiligt.
Die Geschichte mit dem Geld ist auch interessant im Hinblick auf die Art, wann welches Produktionsverfahren eingeführt wird. Drei davon wurden bislang entwickelt (vgl. auch Grafik am Ende des Artikels):
- White OLED – Das ist die simpelste und auch günstigste Möglichkeit, ein OLED-Panel herzustellen. Lediglich ein weißer Emitter ohne präzise Maskenausrichtung wird genutzt. Farbe wird durch einen Farbfilter erzeugt. Dieses Verfahren hat aber auch Nachteile: Die Farbreproduktion ist nicht so perfekt, wie sie durch andere Herstellungsprozesse möglich ist. Zudem wird nur eine relativ geringe Lichtausnutzung ermöglicht. Grund dafür sind die Farbfilter.
- Side-by-Side OLED – Der technisch aufwändigste Prozess, um ein OLED-Panel herzustellen. Drei verschiedene lichtemittierende Schichten werden durch eine Maske abgeschieden. Die Verwendung von nebeneinanderliegenden diskreten R-, G-, B-Emittern weist die Vorteile einer hohen Leistungseffizienz und eines großen Farbumfangs auf. Das Verfahren erfordert jedoch große Vakuumkammern und dreimal eine genaue Maskenausrichtung. Probleme beziehungsweise Nachteile: geringe Materialeffizienz und die Schwierigkeit, gleichmäßige dünne Filme abzuscheiden.
- Printed OLED – Dies ist die von JOLED entwickelte Möglichkeit, OLED-Panels zu produzieren. Es handelt sich um eine RGB-Drucktechnologie für die emittierenden Schichten. Diese Technologie soll eine deutlich höhere hohe Materialeffizienz, eine hohe Lichtausnutzung und eine gleichmäßige Emitter-Strukturierung mit sich bringen. Darüber hinaus wird eine kostengünstige Herstellung durch das skalierbare Drucksystem mit hoher Produktivität ermöglicht. Die RGB-Emitter werden alle für die verschiedenen Panel-Größen und Auflösungen mit einem einzigen Drucksystem gedruckt, das das Drucken unter Atmosphärendruck ohne Nutzung einer Vakuumkammer ermöglicht. Die Produktionsvorlaufzeit reduziert sich.
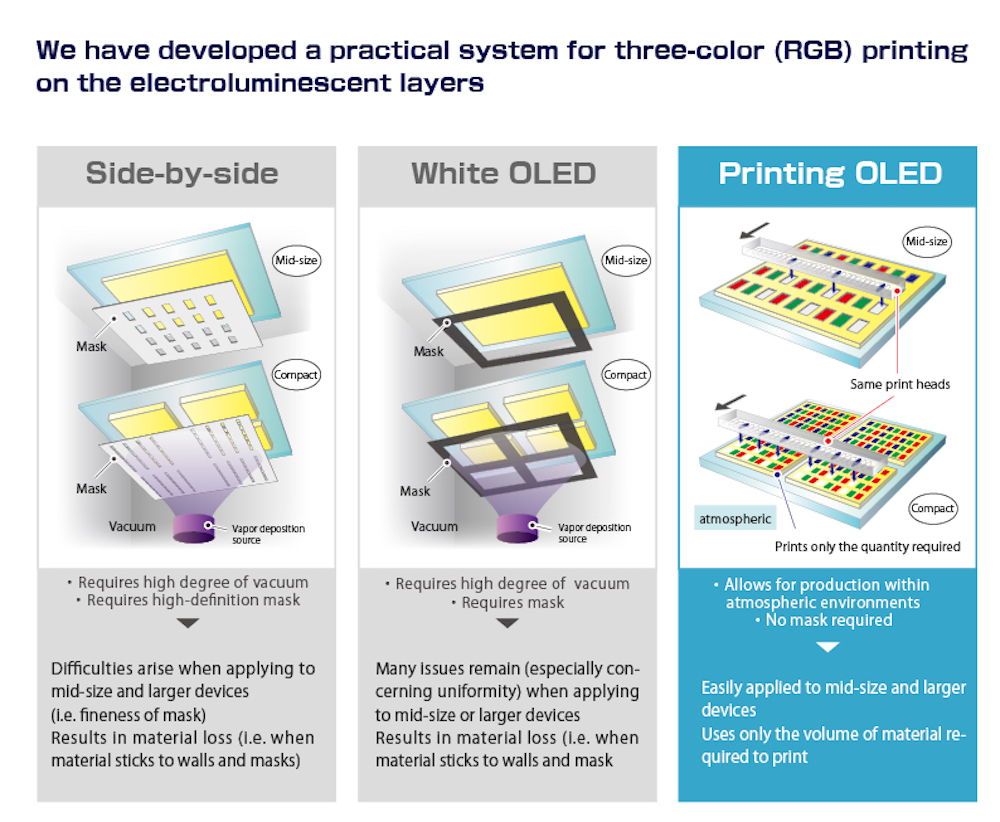